Oil Skimming Equipment Recycles Quench Oil at Midwestern Heat Treatment Plant – Reprinted from Fluid & Lubricant Ideas
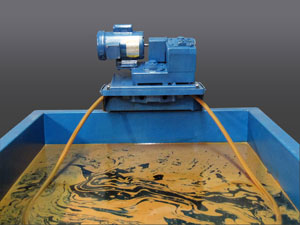
AMAC Enterprises Inc., Cleveland, OH, has found a simple yet effective way to reduce the cost of its heat-treating operations – recycle 100 gallons of quench oil each day, and thus save more than $20,000 each year.
From six employees in the 1950s, AMAC has grown to 90 employees and approximately 130,000 square feet of manufacturing and office space. Forty percent of the operation involves heat treating, and at full capacity the plant can handle 250,000 pounds a day. This process generates 100 to 120 gallons of waste oil and residue each day as the quench oil is washed off before tempering the fasteners.
Sam Torreso, a project engineer, was assigned the task of finding a waste oil recycling system that was cost effective, and easy to operate and maintain. Torreso worked with engineering consultants to develop an oil separation system that included two 1,500-gallon holding tanks, pumps, an outside 99-gallon collection tank, and two Model 5H Oil Skimmers.
All of the washers flow into the first of the two 1,500-gallon holding tanks equipped with a Model 5H oil skimmer, which recovers around 80% of the quench oil. The skimmer removes the oil by using a polyurethane collector tube that floats on the oily surface of the wash water and attracts the oil. The tube is continuously moved up through scrapers, which then remove the oil. Water flows from the bottom of the first holding tank to a second 1,500-gallon tank, where another oil skimmer removes any remaining oil.
To ensure that virtually no water is carried along with the recovered oil to the collection tank, the recovered oil is stored in a small tank connected to the first holding tank. A float control periodically drains 20% of the contents from the bottom of this tank back into the first holding tank, while the remaining 80% is pumped into the collection tank located in the shipping bay. The last part is simple; the oil recycler drives up to the tank once a week, and drives away 15 minutes later with 800 gallons of recoverable quench oil.
“On an investment of this type, we generally like to see payback in about a year and a half. This system was paid off in nine months,” notes Tom Chimples, vice-president and son of the founder.
AMAC was able to recycle quench oil, instead of buying new oil, which provides them with a substantial amount of savings. Chimples explains that, “The company performing the task of re-refining our oil gets the oil back up to the same properties as the new oil, and will provide a certificate to back up this claim. It doesn’t have quite as long a life span, but as it stands now, we don’t need to make any new oil purchases.”
Washwater Systems Kept Oil Free with Skimmers
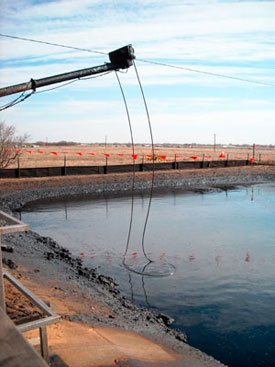
PROBLEM: Centrally located in Fulton, IL, Drives Inc. manufactures power transmission chains, conveyor components, and helical augers for movement of granulated solids. Heat treating at 1,600 degrees F, quenching and tempering at 750 degrees F are sequential processes in producing small parts of requisite hardness and toughness.
One wash system is required to remove cutting oil from the parts before heat treatment, and a second separate wash is necessary to remove quench oil prior to tempering. Wash water is conserved by recycling and must be kept oil-free.
The question in the original plant design was, “What kind of oil removal equipment would provide substantial recovery and assure washwater free from interfering oil content?”
SOLUTION: Following a review of several methods, a skimming process based on the affinity of oil for plastic was selected for both systems. Each skimmer is comprised of a plastic tube, which floats on the surface of the water. The oil collects on the tube; then it is removed by an overhead pulley and scraper mechanism.
A collection tank is sits beneath the pulley mechanism. The separation of water and oil occurs naturally in the tank, forming the characteristic oil film. Clean water is removed from below the surface, and oil is removed continuously by the skimmer.
For the Model 6V tube skimmer, the skimmer mechanism is enclosed in cast-aluminum housing. The assembled unit weighs about 125 pounds and is placed on a column and boom support, which raises the unit some 6 feet above the water surface.
A closed-loop tube, made of a specially compounded polyurethane plastic that attracts the oily waste, is looped through two pulley wheels that have multiple scrapers placed between them to remove the collected oil from the tube. The scrapers conform to the tube curvature and the oil falls into a retention basin. The first pulley serves to align the tube into a horizontal run for the scraper. This pulley is unusual in that it is powered by a motor drive, so as to turn at a peripheral velocity to match the movement of the tube. Movement of the tube is imparted by the second, or drive wheel – this wheel is driven by the motor and is designed to have a firm, non-slip grip on the oily tube.
The grip is attained by 24 ceramic “fingers” alternated in position around the wheel. The ceramic is made with a hard alumina component, which resists abrasion from metallic inclusions, grinding compounds and dirt.
At Drives, the washwater collection tank for the shop oil removal uses two skimmers. The residual oil is stored and periodically sold.
The clean water is removed and returned for recycle. The quench oil, on the other hand, is collected by one Model 6V skimmer and returned to the quench oil tank. This oil is clear and light colored. Estimates are made that more than 75% of the quench oil is saved by this recovery.
The post-quench washwater is returned to its circuit by a double decanting, which not only skims but also separates trace oil in a second tank. The water in both systems is renewed about every six months in a scheduled preventive maintenance program.
RESULTS: The skimming equipment has logged a relatively maintenance-free history. Periodic updating has been easy since improved components are made to fit the previous design. Water quality is high, and the wash process is satisfactory.