Extending the Life of Wash Solutions – Reprinted from Finishers’ Management
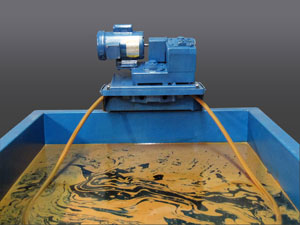
Simple things we learn early in life might well apply to a basic need of the parts washing market: To look good – wash well before you “dress.” Washing metal parts is a necessity prior to painting or plating: If the wash is not properly prepared and foreign substances are not removed from the metal in the wash phase, the finish – the “dress” – may not hold properly, and it may not wear well.
Essentially, the wash is an imperative step in the process. And, as one manufacturer of parts washers discovered, a good oil skimmer is critical for the success of washing metal parts.
OEM Suggests Installation of Oil Skimmer
Oils can adversely affect the final outcome of metal parts production. Used during various stages of the manufacturing process, including stamping and machining, oils can adhere to the metal parts. If this oil is not removed, poor adhesion can occur during painting or plating. Thus, removal of the oil from the part is critical in the wash stage.
As the wash stage removes the oil, it accumulates in the wash solution. This accumulation contaminates the wash solution resulting in frequent bath (wash) recharging or improperly cleaned parts.
These problems lead to ever increasing expenses that include disposal of the contaminated wash solution, additional use of chemicals, costly downtime, and increased labor.
A Midwestern parts washer manufacturer, is quick to acknowledge the critical importance attributed to a wash that is free of floating oil. For more than 15 years, it has been specializing in designing and manufacturing parts washing systems that are tailored to perform to high standards, which include a wash that is free of foreign substances, such as oil, which will adversely affect the painting and plating process.
To correct the costly problems of oil accumulation in the wash, the company provides for the installation of an oil skimmer when supplying washers for customers. After reading about various skimmers on the market, it sought help from Oil Skimmers, Inc., in Cleveland, OH.
They tested and installed a Model 5H oil skimmer. The skimmer effectively removes the oil, thus extending the life of the wash solution while maintaining product quality – a benefit they considered when selecting Oil Skimmers for their operation.
How the Oil Skimmer Works
The fully automatic skimmer is simple in design, yet offers rugged construction. Oil adheres to the outside of a closed-loop tube as it is slowly drawn across the surface of the water, adjusting automatically to changing water levels. The oil-covered tube passes through scrapers that remove the oil. The clean tube then returns to the water surface to collect more oil. The recovered oil flows into a collection container and is virtually water-free. Custom mountings can be designed to meet each customer’s unique specifications.
“With the addition of the Model 5H, we have happier customers. The metals are cleaned of oil, we’ve saved the customer time and money, and the final plating or painting will ultimately adhere better, look better, and last longer on the metal parts,” said the director of engineering.
Ensuring Quality
One of their customers satisfied with the results of the skimmer is a manufacturer of modular merchandising systems for the convenience store industry.
According to their plant engineer, installation of the oil skimmer accounted for less downtime. “During the operation, we monitor the quality of the bath,” he said. “If the concentration of contaminates becomes too high, we must stop the operation and clean up the wash. Oil is one contaminate that must be kept to a minimum. The present unit we’re using from Oil Skimmers, Inc. does this. It removes nearly all the oil from the wash. Other types of oil skimmers we tried didn’t offer the most satisfactory results.”
Because the wash is cleaner, they also notice better parts cleaning, less use of chemicals to combat contaminates, and better salt spray test results. “When we test painted samples in the salt fog cabinet, we test the effects of paint being assaulted by years of wear and tear by salt and heat. We’ve found that by using the skimmer, and eliminating oil contaminant’s, we get better test results” Another benefit of using a well designed oil skimmer is that the process is less labor intensive. “Downtime to recharge the water requires additional labor to restart the bath. Plus, we don’t have to monitor the wash as often, since we’re putting in fewer chemicals. I also found that this oil skimmer can work unattended 24 hours a day. It just keeps doing its job without the need for someone to watch it.”
While curtailed downtime and intensity of labor account for considerable savings, the biggest savings result in the use of less chemicals in the wash system. In addition to cost savings, the major benefit of a well designed oil skimmer is the quality of the end product. “Quality is an important tool in maintaining customers when our customers get metal parts that will withstand years of exposure to heat and other elements, they’ll be back.”
“The benefits far outweigh the initial cost of the investment. There is immediate cost savings in production. But we also see an improved product appearance. And the quality and the longevity of the finish on our shelves has also improved. The real beauty of it, is that the oil skimmer just keeps on going. No maintenance problems, no breakdowns … it just keeps on going.”