Plant has Cleaner Discharge and Resells Oil
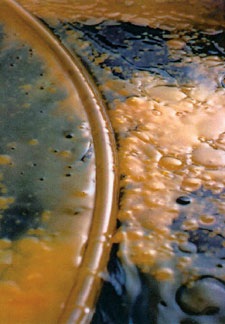
PROBLEM: A polyvinyl chloride resins plant discharges oil into its wastewater. The oil, which is used in the polymerization process, frequently exceeds state limits in the wastewater, which could mean a $53,000-per-day fine. To avoid this, the plant has been metering its discharge from a sump into the public water system in smaller amounts — a costly and inefficient answer. Additionally, the company wants to resell the separated oil, but it is now wasted as part of the discharge.
The plant, which produces 185,000 pounds of resins each year, needs a way to separate and remove the oil from its wastewater.
LIMITATIONS: To meet safety, cost and efficiency goals, the plant needed a solution that could run without an operator and be installed without reconfiguring the current wastewater collection-and-discharge system. The solution also had to be low maintenance and long lasting.
SOLUTION: Oil Skimmers Inc., installs a Model 6V Brill™ oil recovery system, which meets the chemical manufacturer’s needs by:
- Fitting into the current wastewater system: Oil Skimmers can customize each installation. In this case, Oil Skimmers creates a mount system to hold the Model 6V at the edge of the sump. The machine’s collection tube is fed through two small holes cut into grates covering the sump.
- Collecting and separating the oil for resale: In a unique anticlogging design, the Model 6V has a specially formulated plastic tube that attracts and collects the waste oil as it floats on top of wastewater. The oil sticks to the outside of the tube, which then passes through a scraper system that removes the oil. The separated oil flows by gravity into a storage drum. The machine then returns the tube to the wastewater for another round of collection.
- Reducing oil in wastewater: The Model 6V can pick up 10 gallons to 60 gallons of oil each hour.
- Allowing independent operation: The Model 6V Brill™ operates independently and is set on a timer to run during the plant’s five-days-a-week operation. If needed, the Model 6V could run 24 hours a day, seven days a week.
- Providing durability: The Model 6V’s internal components are made of high-strength steel and bronze for durability. External parts are made from abrasive-resistant ceramic. The machine has a 25 to 30 year lifespan.